High-efficiency, low-emission biomass cogeneration plant for secure heat supply
We are accumulating even more experience that can be useful for Ukraine. Therefore, we have prepared an interesting and useful long read.
Hillerod Forsyning, the Danish utility company of Hillerod city, manages a major district heating system that includes the new 28 MW wood chip-fired cogeneration plant designed for a maximum generator terminal power of 5.2 MWel.
It is the largest biomass cogeneration plant with Organic Rankine Cycle (ORC) technology built by Polytechnik in Europe.
Austria-based Polytechnik became the contractor for the supply and installation of a biomass cogeneration plant on a turnkey basis.
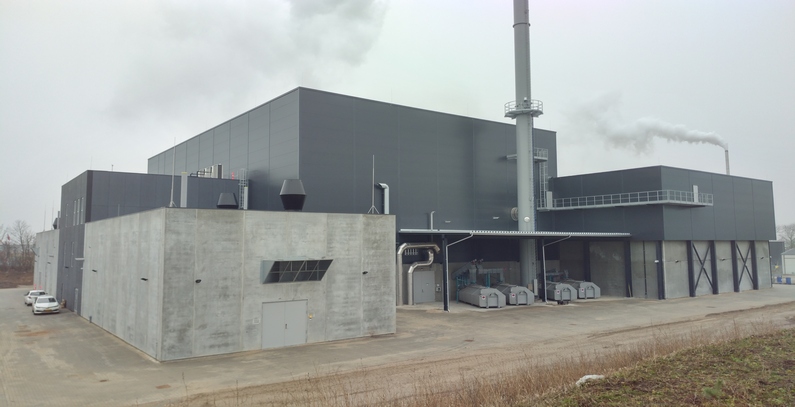
Features of the construction
The boiler system consists of 2 firing and boiler lines working in parallel. This ensures a nearly perfect availability and high reliability. As Polytechnik plants can in addition be run in a broad power spectrum, the distribution over 2 lines leads to a very large control range. Depending on the fuel composition, the plant can be operated in the load range from 15% to 100%. Even in summer, the Polytechnik plant can still be run with a load of approx. 50%. Peak loads are easily buffered and balanced by a buffer storage unit with a storage capacity of approx. 600 MWh.
Raw materials
The Hillerod Forsyning biomass cogeneration plant burns burns exclusively wood chips made from untreated residual forest wood.
Logistics
During installation and building planning, attention was paid to maximum efficiency in fuel logistics. The wood chips are supplied by truck. They are weighed at first, and during each delivery, a fuel sample is taken and analyzed in addition. After concluded assessment and acceptance of the delivery, the fuel is tipped directly into a low-positioned fuel bunker. From this tip-down bunker, the fuel is distributed in the fuel storage by means of two redundantly designed indoor cranes.
A smart logic ensures optimal mixing of fuels with different textures in this process so that the firing system can always be fed with nearly identical fuel quality.
The entire bunker therefore has a fuel capacity for 7 days of full-load operation. The proven, robustly designed and hydraulically actuated walking floors and cross conveyors supplied by Polytechnik have been used for fuel conveying.
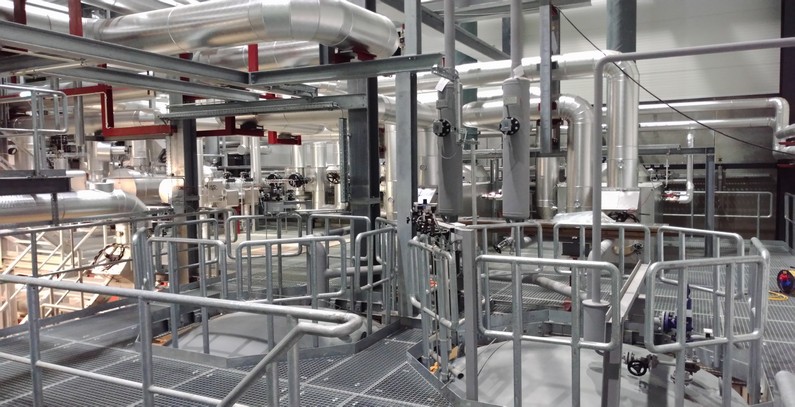
Combustion process
The Polytechnik firing units, which are each equipped with an adiabatic combustion chamber and a hydraulically actuated push grate, form the centerpiece of the plant. The generous dimensioning of the combustion chambers ensures complete combustion of the wood chips with minimum emissions, even in cases in which the fuel has a moisture content of over 50%.
Combustion takes place in several steps:
- Feeding of combustion air and of recycled flue gases into the combustion chamber occurs via several fans that are controlled individually by means of frequency converters. This enables accurate control and monitoring of the combustion chamber temperature, on one hand to ensure complete burn-out and on the other hand to prevent the formation of carbon monoxide or thermal nitric oxides to a large extent.
- After fully completed combustion of the wood chips, the hot flue gases flow through the two thermal oil boilers. Here, a large part of the thermal energy is transferred to the thermal oil circuit. In this process, the thermal oil is heated to approx. 312°C. Each of the boilers has a nominal output of 12.5MW.
Environmental aspect
Let’s talk about flue gas cleaning and flue gas condensation. Pre-separation of fly ash from the flue gases occurs by means of multi-cyclones. Separation of particulate matter from the flue gases subsequently takes place in an electric filter.
Through the use of a condensation system, the intrinsic dust content of the flue gas is already reduced to an extent that the statutory limits can be complied with. Nevertheless, Polytechnik has installed an electric filter upstream of the condensation system. The formation of sludge in the system is reduced significantly as a consequence and the condensation system has a much longer availability.
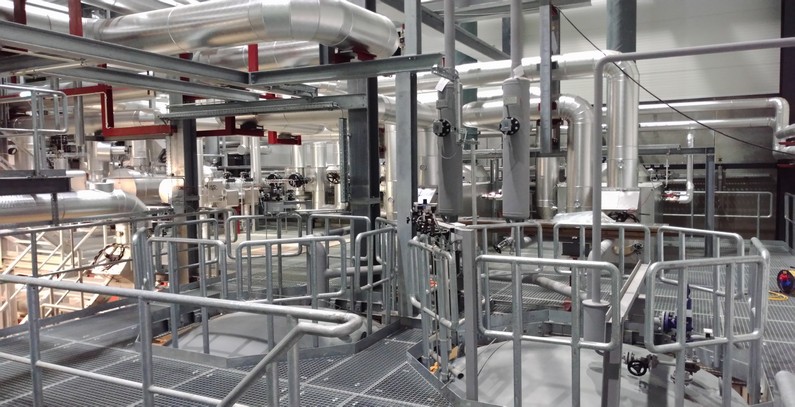
Efficiency optimization by means of heat pumps
At the customer’s request, Polytechnik installed an additional heat pump by means of which the flue gases can be cooled down even further after condensation. The heat pump has a COP value of >5. Hence, an additional heat of up to 2400kW can be generated for an electric drive power of approx. 400kW.
Power generation with ORC
ORC modules have numerous advantages compared to conventional steam turbines. For example, no superheater is required by the plants. Compared to steam power plants, they are run at a significantly lower operating pressure, the medium is not corrosive and does not have to be treated, and water will not be consumed continuously.
In the cogeneration operation, an ORC module can achieve efficiency levels that are similar to the ones achieved with a backpressure or extraction condensation steam turbine. Besides, ORC modules can be operated in a large power range and/or at a very low partial load and started in a fully automated way. Each of the two ORC modules in Hilleroed has a generator terminal power of 2,600kW. ORC modules are equipped with directly coupled asynchronous generators by default.
Control and regulating technology, process visualization
Polytechnik plants are controlled via a Siemens SPS. All operating data are visualized and saved chronologically. In Hillerod, all signals are in addition transferred to the control center of a nearby gas power plant.
All Polytechnik plants can be monitored via remote control. The customer’s staff and the Polytechnik team can access the visualization at any time and from any location via the internet and monitor the operating parameters.
Success
After two years of construction, the biomass cogeneration plant started delivering heat to the district heating system in August 2016, while generators started feeding electricity into Denmark’s public grid on September 8, 2016. The facility has since been running without interruptions.
With regard to operation at nominal load and fuel moisture of 45%, approx. 27.5MW of useful heat and approx. 3.5MW of power (net) are generated by the entire plant for a fuel heat output of 28.6MW. The plant efficiency, therefore, amounts to approx. 108.5%.
Additional information
The boiler house was planned and built taking into account the necessary social spaces, in particular accessibility for people with disabilities and places for employees rest. The project also has a pleasant ergonomic design. The technical equipment of the building meets the highest standards, an elevator system, barrier-free sanitary units, a central ventilation system and air conditioning, as well as a fire extinguishing system with low expansion foam extinguishing stations.
Source: Balkan Green Energy News.