90,000 tons of biomass is burned by a German CHP plant with a PMSXpro process control system
The modern and powerful thermal power plant in Wiesbaden has a very large boiler that burns about 90,000 tons of biomass — wood waste at temperatures up to 1100°C.
Characteristics of the project
- The power station, erected on a 2.3-hectare site, works in combined power and heat mode.
- The fully enclosed fuel storage hall, with a surface area of 1,944 m2 and a height of 13.5m, provides a storage volume of 6500m3 and holds 1300 tonnes of fuel, enough for around 3.5 days or 84 hours. The external fuel preparation site is just 300m away.
- The boiler house stands on a base plate of 900m3 concrete, has a surface area of 866m2, and a height of between 18.8m (low part) and 28.6m (high part).
- The boiler house contains 200 tonnes of steel, and the 280-tonne boiler support structure holds the 730-tonne boiler.
- Immediately next to the boiler house is the complex flue gas cleaning plant with a 46m high stack.
Output
Every year, the station will produce around 55 million kWh of electricity and around 154 million kWh of district heat from the 90,000 tonnes of biomass.
This corresponds to around 4% of the city’s current power and heat requirements, and could theoretically supply 12,000 homes.
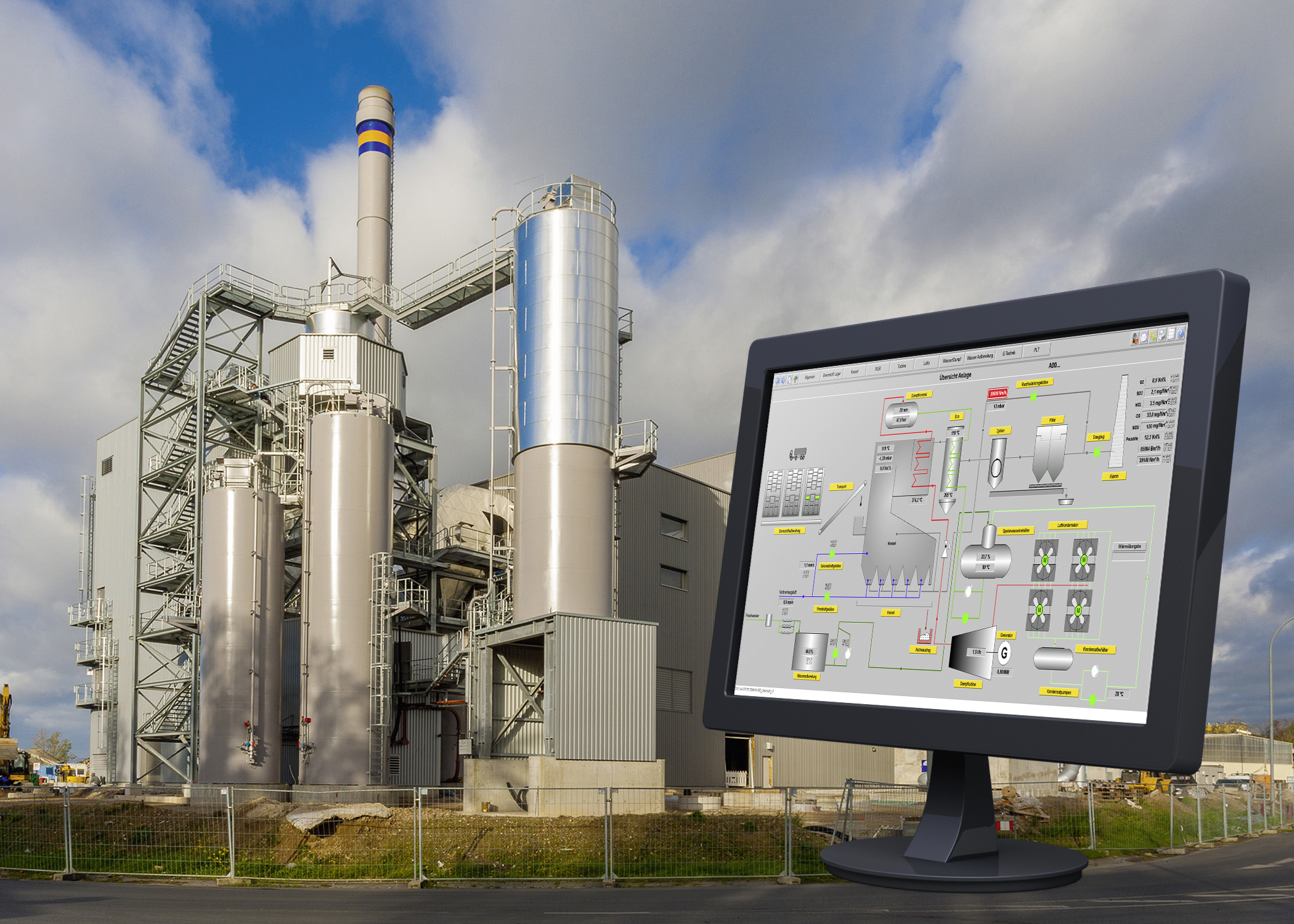
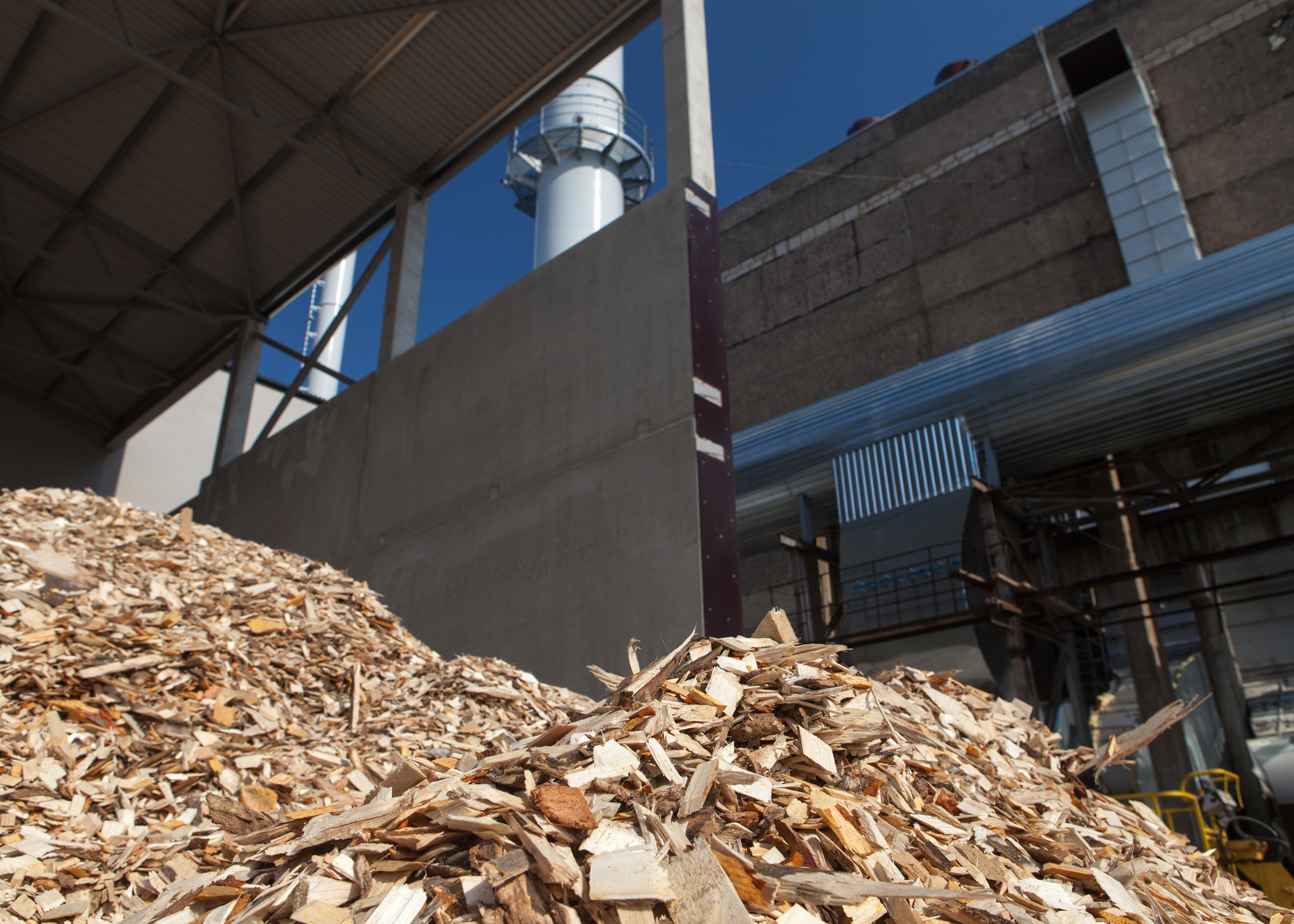
Emissions reduction
Спалювання біомаси як відновлюваного ресурсу призводить до скорочення викидів CO2 Combustion of biomass as a renewable resource leads to a CO2 saving of around 94.7 million kg per year.
Emissions from the station comply with the strict limits of the 17th Federal Emissions Protection Law (BImSchV).
Biofuel supply
The majority of the waste wood comes from bulky refuse collections. The comminuted material, free from coarse impurities, is transported by truck to the station’s fuel storage hall, where it is deposited in storage containers. The fuel is then conveyed by wheeled loaders to push-feed floor units, from where it is automatically transported to metering and storage containers in the boiler house for supply to the furnace.
Combustion
Via an automatic feed, the fuel reaches the technical heart of the station – the furnace chamber – where it is burned at temperatures of 950-1100°C on a multizone, air-cooled feeder grate with automatic intake. The combustion heat output is around 46 MW.
At this point, the nitrous oxides are already largely removed from the flue gases, primarily via flue gas recirculation and secondarily by urea addition. The hot flue gases now flow though the boiler passes to generate steam, and are then freed from further contaminants in a complex flue gas cleaning plant.
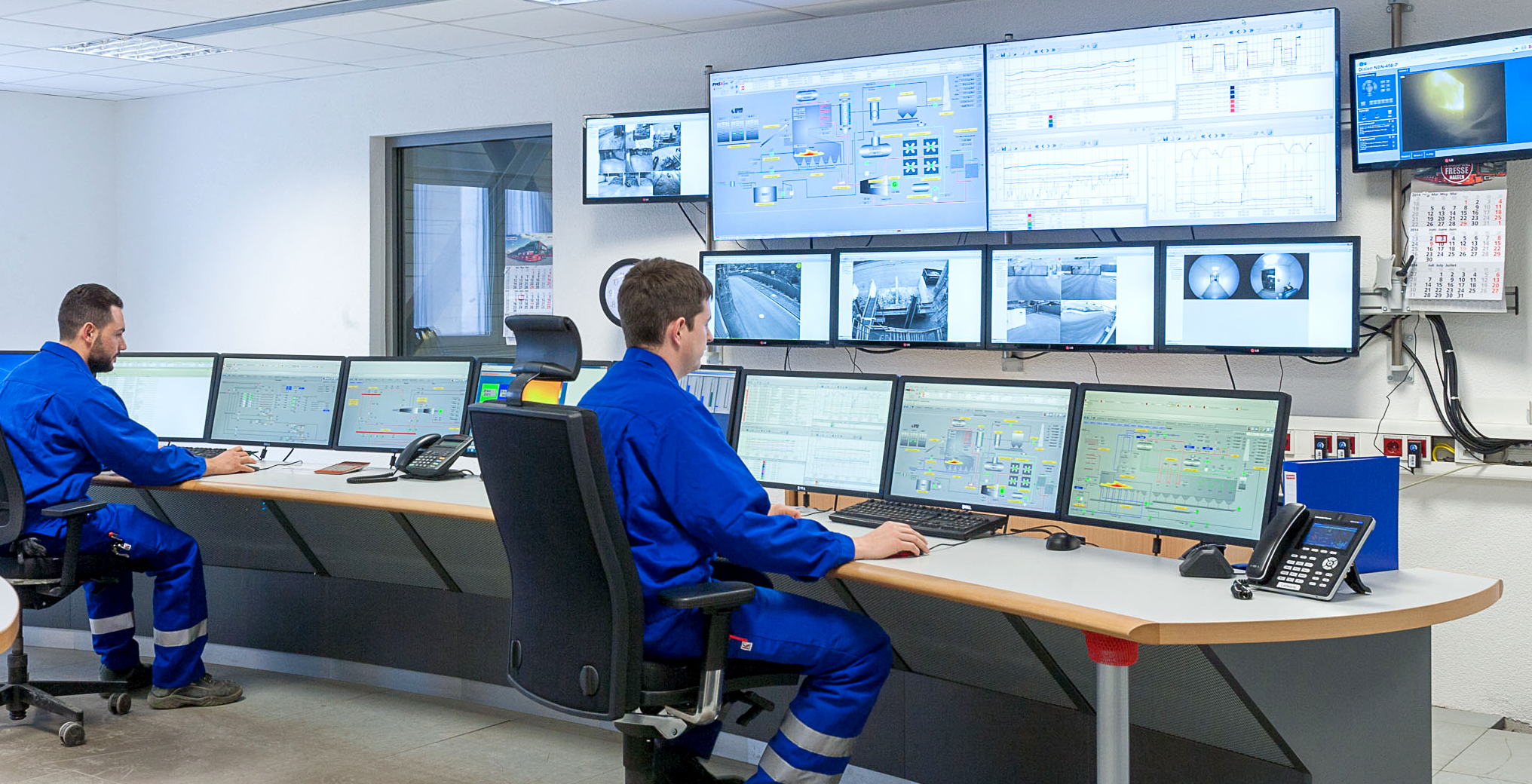
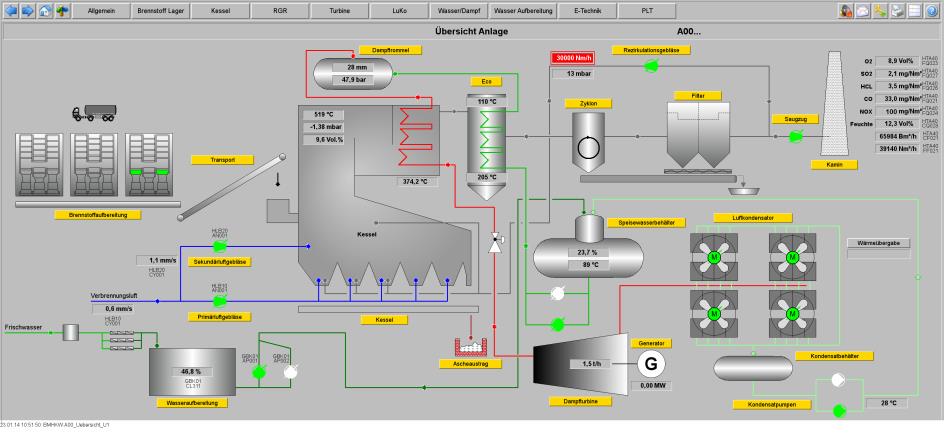
Electricity production
The hot steam generated by the combustion of the biomass is extracted from the boiler and supplied to the turbines. The mechanical rotary motion produced in the turbine is converted by an alternator into electrical power, which is then transformed up to medium voltage (20 kV) in an in-house transformer. A 2km cable feeds the resulting CO2-neutral power from renewable energy into the power network.
When the power station is not producing electricity, it is supplied with power via the infeed cable. An uninterruptible power supply (UPS) and substitute generator ensure that, even on failure of the public power network, the station can be transferred into a safe operating state.
District heat generation
After the high-pressure steam has been reduced to a lower pressure in the turbine, it is supplied to the heating condenser, which brings the heating water for district heating to temperature. An underground, heat-insulated pipe system feeds this heating water into the district heating connection network.
The heat is delivered to the consumer via a heat exchanger in the form of a transfer station. The operating temperatures for output are 70-100°C at an operating pressure of 10-15 bar.
PMSXpro process control system
The combined heat and power station is monitored via the PMSXpro process control system from ME-Automation Projects, based in Fuldabrück.
Guaranteed high reliability is essential, and this is ensured by the PMSXpro process control system, using fully duplicated automation stations and also duplicated process servers for total redundancy.
The duplicated automation stations are Mitsubishi Electric control units from the MELSEC System Q series, which ensure safe automation of process procedures and monitor the fuel store, combustion and boiler, through to the flue gas cleaning. The control system components communicate with each other via an error-tolerant FO network. This control system network is connected via an application server to the office network, so authorized users in the office to have access to the PMSXpro process control system via a secure connection. For remote service, two internet access points (DSL and UMTS) with tunneled VPN connections are available.
The ME-Automation Projects’ scope of supply includes:
- The network cabinets and distribution racks, their construction, and the associated electrical installation of the LV system and entire control system network.
- The control system components, consisting of control and monitoring stations, process servers, archive servers, application server and engineering stations, and all automation stations with a total of over 6000 inputs and outputs. All automation stations are coupled together via a separate FO network and each has a Profibus Master for connection of further Profibus units.
- Complete programming of the automation stations (including safety control systems) and control system components for all process-technical structures.
- FAT (Factory Acceptance Test) for each structure.
- Cold and warm commissioning and trial operation.
- Documentation to VGB R 170 C.
The PMSXpro process control system, certified to VGB R 170 A, B and C, from ME-Automation Projects ensures 99.9% utilization in the Wiesbaden combined heat and power station, which equates to 364 days and 15 hours per year.
It took 18 months to build such a powerful facility. However, the planning and approval stages took more than three years.
The construction cost was 55 million euros.
Source: ENGINEERLIVE