Huelva — one of the largest biomass power plant in Southern Europe
In this article you can find information about the technical and environmental aspects of the Spanish power generation plant with a capacity of 50 MW that can meet the electricity needs of a city of 360,000 inhabitants.
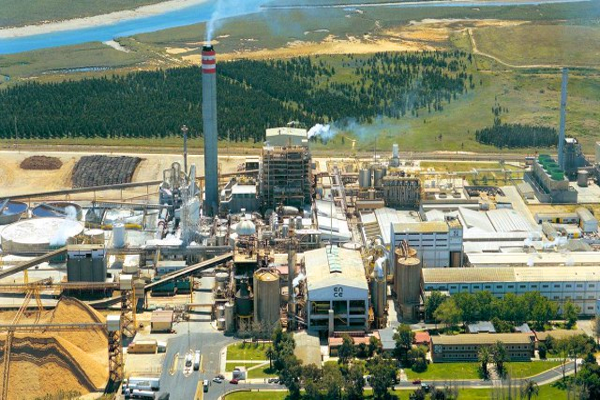
Spain’s and southern Europe’s one of largest power generation plants using forestry biomass provides a power output of 50 MWe. It is worth noting the high cycle design efficiency in terms of primary energy fuel usage for the power production. Currently, stable and constant values of electric out, out to the grid are being registered.
Energy for 360 000 inhabitants
The guaranteed power production is around 370 000 MWh per year obtained from the turbine, which in turn is driven by superheated steam at high pressures. Some 366 000 tonnes per year of biomass are needed for this purpose. The production equals the power demand of a city of 360 000 inhabitants.
600 000 tonnes/year of processed biomass
The plant takes up an area of around 65 000 m2 and is composed of two main operative parts:
- processing park,
- power island.
The processing park is where the treatment of the incoming forest biomass; forest residues, energy crops, logs and eucalyptus stumps takes place at a pace of 95 trucks per day. The processing capacity of the processing park is estimated to be around 600 000 tonnes per year; this challenge has been overcome thanks to the use of advanced technology for the pre-treatment and the internal logistics of biomass.
How is the process going?
Once unloaded from the truck and crushed, the biomass goes through half km of conveyor belts until it arrives at one of the two-day storage silos.
One of the main characteristics of the processing area is flexibility in managing different types of biomass without affecting production. This has been achieved thanks to the arrangement of the equipment within the circuit. Inside the biomass processing park there are three zones:
- Crushing process: Including two single rotor fast crushers, a double rotor slow crusher and a trench for the crushed biomass. On arrival to the treatment park, the received biomass can be irregular due to harvesting or collection technicalities in the field or forest; here it is processed until it fits to the right size for the boiler’s fluidized bed technology. Biomass moves on a variable speed mobile floor which discharges onto a subterranean conveyor belt that takes the crushed wood to the screening building.
- Screening process: It has different separators and sieves to remove metals and stones that might harm the boiler in case they went through. When they exceed the specified size, they are re-processed in a mill.
- Distribution process: Biomass with the right size is transferred to a distributor that leads it either to the boiler’s silos or to the storage silo.
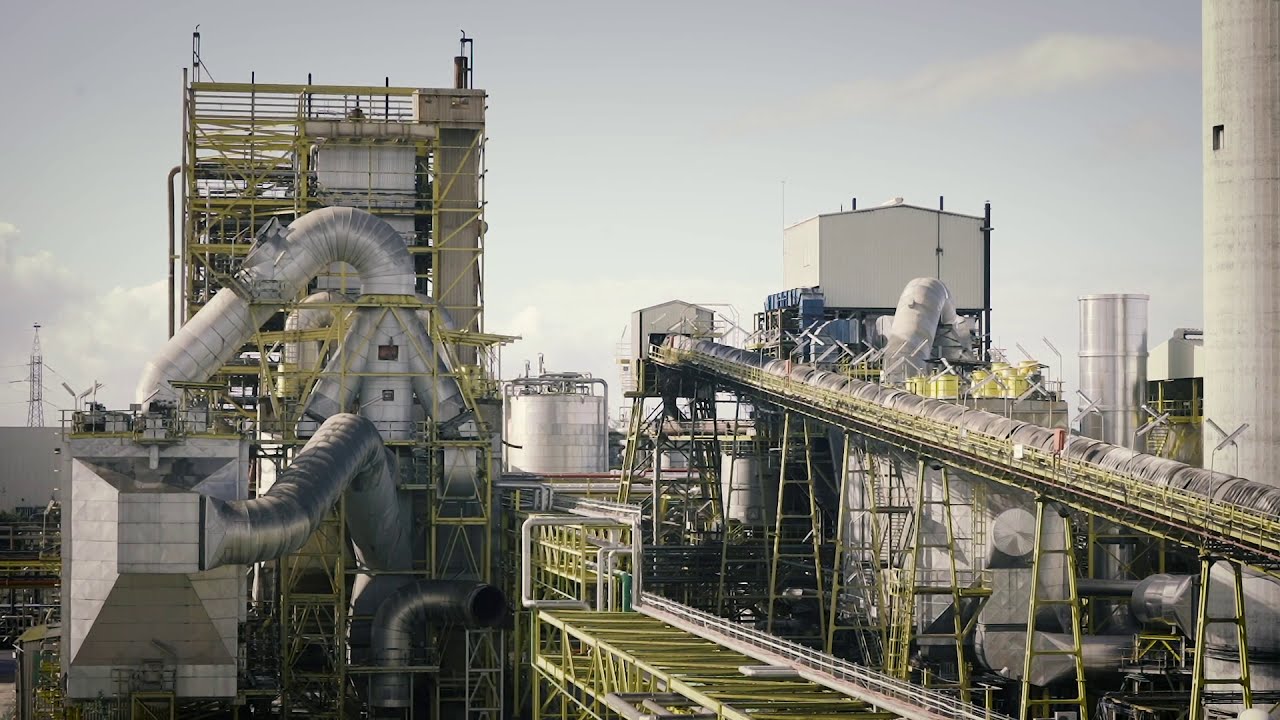
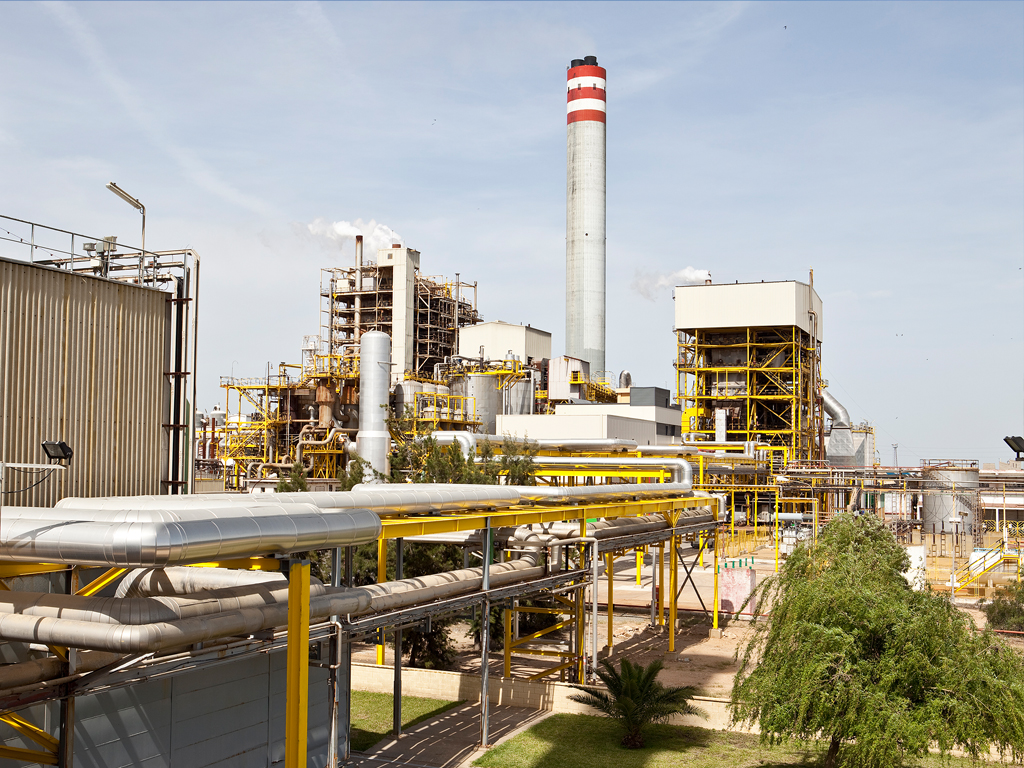
Fluidised bed technology
Correctly-sized biomass is fed into the boiler’s furnace via screw augers and a feeding hopper to fall onto the sand fluidised bed, where combustion takes place. Fluidisation is achieved thanks to the nozzles situated at the furnace’s lower part, which inject the primary air that causes the suspension of the sand. This primary air covers 35 – 40 percent of the oxygen needed for combustion, hence more air (secondary and tertiary) is injected into the furnace in order to guarantee full combustion.
Gas Cleaning
The combustion gases cross two electrostatic precipitators and their induced draft fans in order to eliminate suspended particles before being led to the flue. Moreover, to reduce NOx emissions, a non-catalytic selective reduction system (NCSR), which reduces nitrous oxides to molecular nitrogen with ammonia, is used.
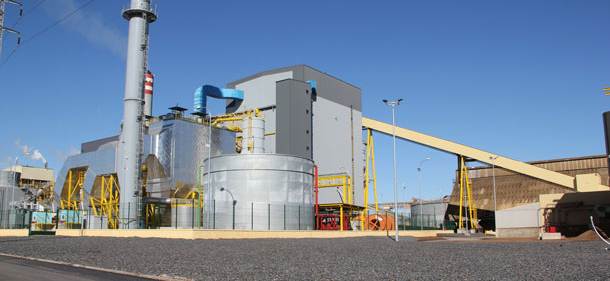
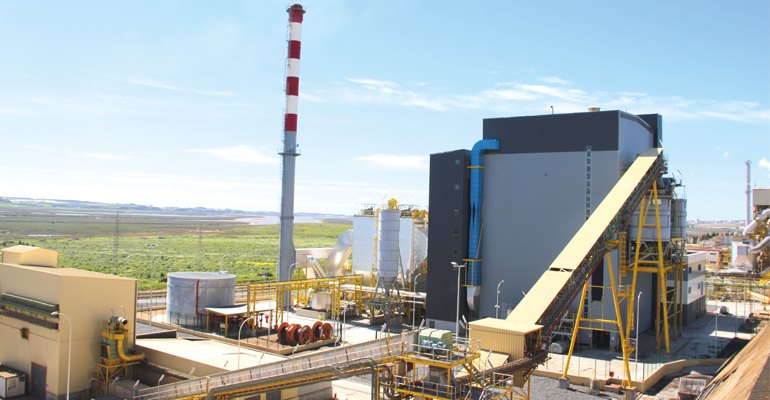
Auxiliary fuel
To supply the water, steam, natural gas, fuel-oil and propane needed during start-ups, the plant is connected to ENCE’s factory through a pipe rack.
Natural gas is used as auxiliary fuel is filtered and its pressure and temperature are prepared for boiler entrance in the Regulation Station, where it enters at a pressure of 35 to 72 bar and leaves at 4 bar, which is the burners operating pressure.
Water-steam circuit
Raw water coming from the factory is led to the service tank and from there to the water treatment plant to produce demineralised water for the cycle. This water is stored inside the demineralised water tank, being pumped into the boiler as an input to make up for losses from purges.
The cycle starts at the water feeding tank. This water is pumped by the feeding pumps through the economiser – at saturation temperature into the steam drum. From there, the saturated liquid fills through natural convection the furnace walls where the evaporating surfaces are placed, to go back to the drum as saturated steam. Inside the steam drum, liquid and steam merge and steam is separated to increase its energy in the superheaters. After various superheating stages, steam at 500º C and 101 bar is obtained and sent to a turbine where it expands to reach 0.05 bar and 33º C, which are the condenser’s vacuum conditions, using thereby steam’s energy to generate electricity. A by-pass valve upstream the turbine protects it in case of turbine trip.
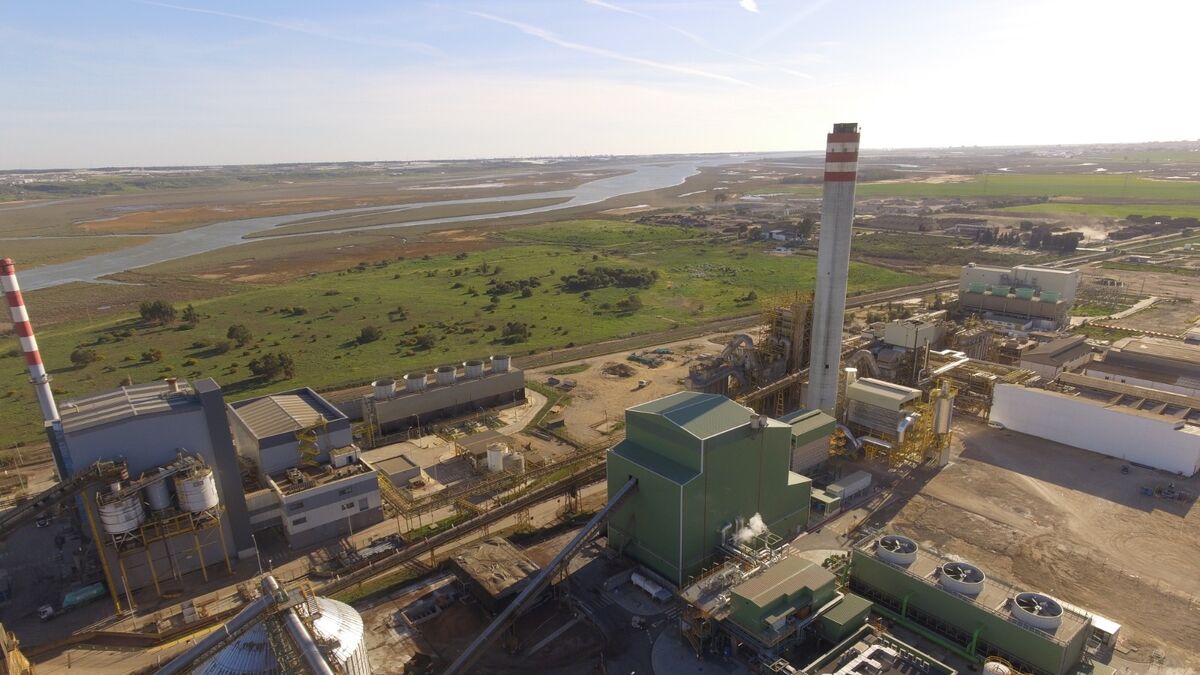
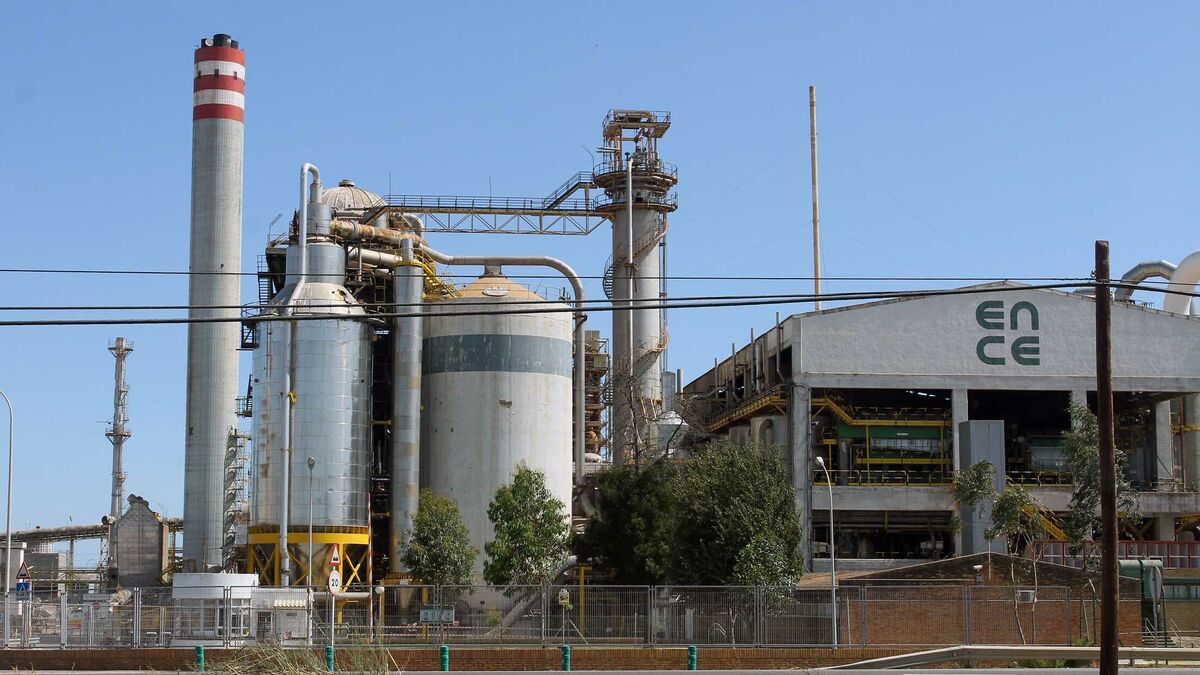
Turbine
The turbine has five high and medium pressure steam extractions used to heat the condensate in the preheaters I and II, heat and degas the feeding water in the feeding water tank and obtain steam for the ash blowing and boiler burner systems.
Two vacuum pumps extract the air and other incondensable gases from the condenser, generating a vacuum that improves the cycle’s performance. In addition, circulation pumps move water at 12 000 m3 per hour from the refrigeration tower pool to the condenser water boxes in order to absorb the heat left by the steam in the change of phase. This causes an increase on the circulation water temperature that refrigerates with the air current in the refrigeration towers. The total process is controlled and monitored from the control room.
Environmental considerations
The technology used in the plant allows environmental improvements such as:
- It avoids 300 000 tonnes per year CO2 emissions compared to coal plants;
- Its ‘non-catalytic selective reduction’ system allows the reduction of NOx present in the boiler flue gases by half;
- The 70 m stack facilitates atmospheric dispersion of the emissions, guaranteeing suitable air quality for people in the surroundings;
- Control of the particle emission to the atmosphere is achieved through electrostatic; precipitators to purify combustion gases and through the use of closed silos and covered systems to transport the biomass;
- Noise reduction in the plant thanks to the installation of modern measures;
- Uses burners in the natural gas boilers as an auxiliary fuel, avoiding SO2 emissions associated with other fossil fuels.
Plant is owned by ENCE Energía y Celulosa de Huelva. In addition, ENCE Group is also a supplier of sustainable forest biomass, which is the main fuel. Energy selling into the grid is managed directly by ENCE Group. The project has been built and is being managed by OHL Industrial.
Source: Bioenergy International.